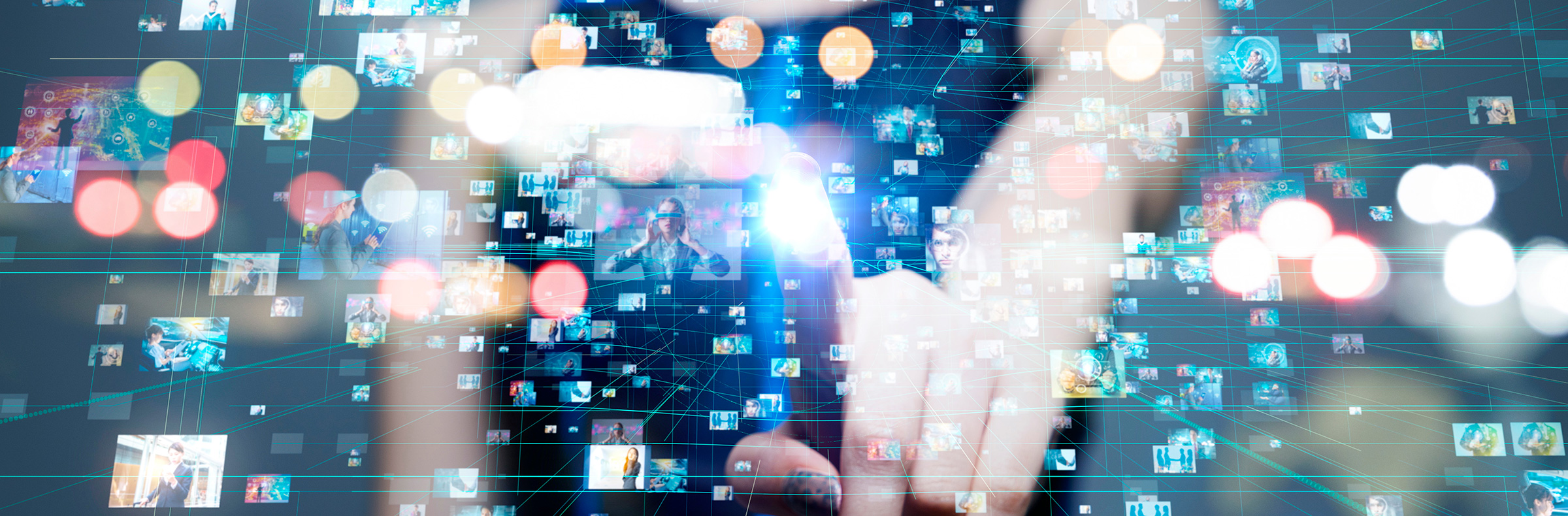
技術情報
2021.05.18
はじめに:
インテクノス・ジャパンは、宇宙・航空・防衛・油圧分野など精密製造プロセスのコンタミ自動監視/清浄度改善のコンサルテーションに特化してきた。近年は自動車とその部品、特にはエンジン・ミッション・ブレーキ・ステアリングなどの流体部品メーカーおよびそのサプライヤーからの、清浄度検査と清浄化コンサルテーションの国内要求も増加してきた。本書は、従来行われてきた旧式の重量法検査(mg/L)での評価から、粒子サイズと個数により数値化される粒子計数検査へ変わった現在と、次世代の自動車部品清浄度検査標準について国際規格や組立集合体異物検査の動向を執筆する。
第1項「自動車部品清浄度検査の標準化」では、VDA19.1-2015 および ISO16232「Road Vehicles — Cleanliness of components of fluid circuits 」に記載された自動車部品の清浄度検査に用いられる技術について、その概要を説明する。 (標準は 50µm 以上から分析)これら規格は主として、部品の表面からコンタミを抽出する方法と定量的分析・実践方法を記載している。あくまで部品単体の清浄度を評価するもので、エンジン・トランスミッション・ステアリングなどの組立集合体の出荷保証に適応されるべきものではない。
第2項「駆動系ユニットの異物検査動向」では、エンジンなど組立後の駆動系ユニットやセミアッセンブリーしたポンプ・バルブなど、出荷保証に最適な流体部品集合体の流体中微少異物を計数する最新の検査システムを解説する。その検査システムとは、ISO11943「液体用オンライン式自動粒子計数システム」(PDS.TM)を活用して、ISO4406「固体微粒子に関する汚染度のコード表示」(ISO 等級)で判定するものだ。このシステムは、出荷機能テスタで製品内部の部品を通過する流体を検査・監視することで組み立て集合体の出荷保証に適応されている。 (標準は>4µm(C)、>6µm(C)、>14µm(C)、3 粒子レンジ)
第1項「自動車部品清浄度検査の標準化」:~残渣検査:重量法からの脱却、粒子計数法へ~
部品清浄度が自動車業界で求められるようになったのは、Robert Bosch GmbH が ABS やディーゼルエンジン向けコモンレール式燃料噴射システムを生産開始したのが始まりだ。同社は噴射ノズルの径を縮小し、コモンレール室内を高圧にしたことにより、小さな噴射ノズルに生産プロセスから混入したコンタミ粒子が詰まりやすく品質問題となった。
この問題から、旧式の重量法での検査限界が判明し、粒子径数法における部品清浄度検査の誕生へと繋がった。それ以来、自動車システムにおける多くのトラブルは微少コンタミ粒子の大きさや濃度に起因している、すなわち部品の清浄度を把握するのに重量検査では不十分であり、それらの検査では品質と信頼性が担保できないと判断され、部品単体の検査から粒子径数管理が求められるようになったのである(図 1 参照)。
図 1 : コンタミによる損傷要因は重さではなく大きさである。
そして、重量検査ではコンタミによる不具合との相関がとれないことが明らかになり、2005年にドイツ自動車工業会の品質マネジメントセンタから発行された VDA19 で、自動車部品における粒子清浄度検査の有用性が世界的に証明され、これを元に国際規格 ISO16232が策定された。2009 年に発行された ISO16232 は、ドイツ以外の多くの自動車会社とそのサプライヤー清浄度検査の重量法から粒子計数法への移行を後押しした。今日では、自動車会社内に多くの専門役職(多くの場合、部署)が作られ、粒子径数での部品清浄度やユニット集合体での残渣粒子の監視や対策にあたっている。最初に、エンジン・トランスミッション・ブレーキシステムなどの軸受・バルブ・ポンプ・流体部品で採用されたが、ZVEI(German Electrical and Electronic Manufacturers’ Association)によりリチウムイオンバッテリや電子部品の清浄度管理にも粒子計数が求められ、増加の一途をたどっている。
VDA19 初版の発行から 10 年後、ドイツ自動車工業会は規格の改訂と付属書の追加を求めた。その主な理由は、分析結果の比較可能性の改善、及びコンタミ抽出・分析の新技術の追加である。改訂版(VDA19.1-2015)が 2015 年 3 月に発行されると、その内容を世界標準化すべく ISO16232 も改訂委員会が設置された。ISO16232 の改訂版は、2017 年に発行される予定である。今日、この二つの規格が自動車業界における部品清浄度分析の枠組みを作っている。後述する最新のパーティクルスキャナ MicroQuick は、これまでの高額な光学/電子顕微鏡というハードルの高い分析機器の導入を、VDA19.1 や ISO16232 の改訂版に準拠した独自のスキャニングシステムの開発により、コンタミ粒子の分析報告までの流れを一新した。フィルタに採取したコンタミの検出(分類・大きさ・個数)をわずか 2.5分で自動測定する装置は全世界のグローバル企業のファシリティで運用されている。
■ ISO16232:多くのファシリティで人為誤差無く簡単運用できるスキャニング方式
清浄度検査は、一般的に 3 つのステップからなる(図 2 参照)。まず始めに、部品の表面からコンタミ粒子を洗い流す。次に、抽出液を分析フィルタで濾過する。最後に、フィルタを分析し、旧式であった重量検査に加え粒子径とその個数を、さらに拡張分析として特長や材質を評価する。
図 2 : 部品清浄度検査の一般的な構図
STEP 1:粒子抽出
コンタミ粒子の抽出に最も使用される方法は、部品の表面を高圧の流体で洗浄する方法(圧力リンス)である。その典型的な例を以下に示す(図 3 参照)。
図 3 : 圧力リンスの例
他には、超音波槽を用いた方法が知られているが、近年余り使用されていない。超音波エネルギーはダイキャスト部品の組成体を破壊するため、粒子数が増加し誤った分析結果が出してしまうからである。
さらに、内部リンスや撹拌方法もある。これらは、部品の内部表面からコンタミを抽出するのに用いられる。また、VDA19.1-2015 には高圧のエアフローを用いた方法(エアー抽出)が新しく記載されている。これは、液体と接触してはならない部品を対象にしたものだが、まだ定着はしていない。
STEP 2:粒子濾過
ここでは、抽出液をフィルタに真空濾過しコンタミ粒子を堆積させる。発泡膜フィルタやメッシュ膜フィルタ(図 4.1 参照)等があるが、液体への化学的耐性や孔径を考慮し、適切なものを選択する必要がある。また、汚染が高い部品はセグメンテーション、いわゆる段階的なフィルタ採取を行い、最終的に合算する方式が求められる。
図 4.1 :発泡膜フィルターとメッシメン膜フィルターの構造比較(VDA19.1)
硝酸セルロー発泡膜フィルター(8μm) PET メッシュフィルター(15μm)
発泡膜フィルタの構造は、スポンジに似ており濾過能力がメッシュに比べ高い。そのため、全粒子質量の測定に非常に適している。また、孔径がサブミクロンからあり、微少な粒子を測定することが可能である。その反面、発泡膜フィルタは抽出液に分析対象外の微粒子が多く含まれてしまう。そして、カーボンブラックが存在すると暗い背景になりやすい。その場合、粒子を精度良く光学分析することは通常不可能となる。
よって、VDA19.1 は 5µm のポリエチレンメッシュを推奨している。5µm メッシュは、比較的暗い背景になることはなく光学分析に非常に適しており、またポリエチレンは多くの抽出液に化学的耐性があるからである。しかし、孔径が最小 5µm であるため、光学では 25~ 50µm 以上の粒子分析に限定される(図 4.2 参照)。
例えば、50µm 以上の残渣を管理したいのであれば、5µm メッシュを利用し、100µm 以上の管理を実施するようであれば、10µm メッシュで粒子濾過をします。
図 4.2 : メッシュフィルタと測定対象粒子径
図 4.3 : 実際のフィルタイメージ
STEP 3:粒子分析
A_重量検査:
機械工業界の旧式残渣測定であり、今後管理しなければならない微小粒子の残渣試験には全くもって不向きで、現在の自動車部品の信頼性を確保する清浄度検査とは言えない。前提として、閉塞させたり摺動不良を起こす要因は、重量ではなく粒子径に関係するからである。残念ながら国内の自動車製造ラインでの残渣検査としていまだ主流なのが重量法である。しかも、重量での正確な結果を得るためには分析フィルタの前処理が重要で、微小粒子では人為的な差が生じやすい。この方法を用いて 3mg 以下を計測するのは、技術的に困難であることは留意しておきたい。
図 4.4 重量法では機械故障は相関がとれない。
B_粒度分析「粒子計数法」:
VDA19.1-2015 改訂版以降では、パーティクルスキャナ MicroQuick のような簡易的に粒子分析できる装置の採用が認められている。規格改定期間中に VDA19 のワーキンググループは、複数の自動光学顕微鏡および MicroQuick のラウンドロビン・テストを実施した。ラウンドロビン・テストとは、測定者の技量を含めて測定方法や測定装置の信頼性を検証するために、複数の試験機関にて同一試料の測定を行うことである。この比較テストの目的は、テスト結果の同等性を上げるべく測定パラメーターを確立するためであった。その結果、画像輝度および粒子検知の閾値を同一の方法で調整することにより、定量的結果がほぼ同じになることが判明した(図 5.1 参照)。今では、フラットベッド式スキャナは粒度分析において光学顕微鏡と同等に扱われている(VDA19.1 改訂版に記載されたルーチン遵守を条件とする)。
図 5.1 : 光学分析における設定(VDA19.1-2015)
VDA19.1 には、正確な測定結果を得るための装置の設定方法が記載されている。まず始めに、フィルタ背景がグレー値の 50 %になるよう出力レベルを設定する必要がある。次に、二つの閾値を設定し暗い粒子(低閾値)と金属反射で明るい粒子(高閾値)を認識する。VDA19.1 のルーチンには、実際のフィルタ背景に対し低閾値を 70 %・高閾値を 145%に設定することが明記されている。※ただし、VDA19.1 の記述に従う必要が無い場合に、パーティクルスキャナは低閾値を 80 %辺りに設定することで、検出域では小さい25µm の粒子計数の精度が上がる。一方、この設定では 50µm 以上の粒子が実際より大きく解析されることがわかっている。
図 5.2 : VDA19.1 に合致したパーティクルスキャナ MicroQuick
近年、部品品質検査において、25µm 以下の微粒子検査から遠ざかる傾向にあり、エンジン部品の管理を中心に多くの事例で 50µm 以上の粒度検査が標準分析になったことから、低閾値が 70 %と決められたのだろう。(図 2 参照)25µm 以下は部品単体の検査では特例だが、部品集合体の品質保証の領域では、実際に摺動面やクリアランスに影響を与える 4µm からの液体中粒子検査が標準となっている。
パーティクルスキャナ MicroQuick(図 5.2 参照)は、一般的に粒子種類と粒子径・粒子数が表示され、部品清浄度コードで合否を判定することができる。(図 6 参照)しかし、光学顕微鏡やスキャニング方式を含む画像解析では、ハードウエアやソフトウエアが高いレベルにあったとしても、材質特定は推測の域をでない。あくまでも光学式は粒子径と計数を検査ツールであることを理解しなければならない。
図 6 : パーティクルスキャナ MicroQuick での部品清浄度の一般的な表示方法
なぜなら、材質の識別はどの光学システムでも同じく、粒子からの金属反射を捕らえ、光沢のある粒子とそうでない粒子を識別したり外形認識するだけである。この光学による金属の識別は、真値の物質分析ではなく、あくまで推測の域を超えない。特に、粒子の表面が腐食している場合(ほとんどの場合)、金属反射は認識されない。逆に、光沢のあるプラスチックやガラスの粒子は金属反射として認識され、誤った分析結果に繋がる。信頼性の高い粒子分析が必要な場合は、拡張分析である SEM-EDX のような方法で、正確な測定をすることが望ましい。
図 7.1 光学式 VS SEM/EDX (光学式は材質特定には至らない)
最近の SEM-EDX は、5µm さらにはそれ以下の粒子を、高速で多数の材質から自動識別することができる。しかし、生産品の品質検査には時間がかかるので不向きであり、あくまでも拡張分析であることを理解しなければならない。また数千万円の設備投資が必要となり、サプライヤーや子会社にとっては導入やその後の運用が困難である。そこで、インテクノス・ジャパンでは、認定機関による SEM-EDX 分析の受託業務を行っている。当社の受託分析は、粒子別の材質の特定と粒子径・粒子数を報告する(図 7.2 参照)。
しかしながら、VDA19 改訂版は、安価なパーティクルスキャナ装置や簡易な器具を用いた清浄度検査結果において、より良い同等性を示す前進となった。また、50µm 以上の粒子が VDA19 の標準清浄度分析対象となり、25µm 以下の小さい粒子分析は部品単体での検査においてあまり重要ではない、という見解を VDA19 のワーキンググループは示した。
図 7.2 : SEM-EDX による元素組成の結果データ
第2項「駆動系ユニットの異物検査動向」:
~オイル清浄度検査:ボトル検査からの脱却、全数自動検査へ~
自動車・自動車部品分野での新しい開発の取り組みは、排ガス規制・燃費向上・ドライビング性能向上の要求から、ハイブリッド車・クリーンディーゼル・新型エンジン・スーパーチャージャー・アイドリングストップ・ABS・AT の多段階化や CVT 無段階変速機といった流体部品集合体においても、新しい技術の実現につながっている。
従来に比べ、この極めて精密な流体部品を採用している自動車の製造ラインにおいて、これまで行われてきた安易な「洗浄液で洗えばキレイになるだろう」「濾過機を設置すればキレイになるだろう」「バッチでオイル検査しているから大丈夫だろう」という、正確性に欠ける汚染管理や推測的な改善を見直す時代に突入したのだ。オイルの汚染度を表す国際規格 ISO 等級(ISO4406:図 8.1)で、使用部品最小クリアランスの 1/3 程度の粒径を管理最小粒子径と考え、粒子計数法で管理することが精密機械分
野での標準になってきた。そして 10 年前の自動車設計とは異なり、それら新しい流体部品集合体の摺動面や流路に残った数ミクロンの微少汚染物質こそが、初期不良のみならず性能や部品寿命の低下に多大な影響を与えるようになってきたことを認識しなければならない。しかしながら、重量管理・ボトルサンプルでの粒子計測、フィルタリング方式や設備配管設計、またフラッシングの考えが旧式であれば、異物による信頼性低下は否めない。
図 8.1 : トランスミッションフルイド、テスト油で活用されている ISO4406:1999
これからの自動車、特に「駆動系ユニットの異物検査」は、製品に影響を与えるこのミクロン単位の汚染微粒子を各製造プロセスで常時数値管理し、汚染されているものが出荷されるリスクを排除しなければならない。これまでは一部生産品をバッチで抜き取り、検査員が検査室でオイルの清浄度を判定する方法しかなかった。このバッチ検査こそが、自動車産業の異物問題を根本的に解決できない要因の一つであることを理解したい。バッチ検査間隔は様々だが、手間がかかるので多いところで 1 日数回、大半は 1 週間に数回程度での検査実施となっているのが実状である。
このバッチ検査で良しとされている工程管理は、数分間隔で製造している生産ラインにおいて「検査を逃れる製品」の方がはるかに多く、生産品の品質検査にはほど遠いほんの一部の清浄度を測っているにすぎない。この検査システムが日本製品の信頼性を低下させる要因となりはじめていることを理解するべきである。
また、このバッチ検査が正確性に欠けるもう一つの理由は、サンプルの採集方法にある。流体部品を流れるオイル中の微少異物を計測するのに、ボトル採取は不向きであることを認識しなければならない。なぜなら、数ミクロンの赤血球や白血球サイズの粒子個数を計数するのに、人が介在したサンプル採取こそ、検査誤差を生じさせるからだ。海外や精密機械産業の主流は、すでに人為的な採取誤差や二次的な汚染要因を排除したオンラインサンプル(図 8.2 参照)で管理している。これが活用されるべき自動車製造は、リニアソレノイドの摺動・インジェクタの目詰まり・油圧作動・精密軸受へ影響する部品や製品、給油システムであり、世界標準のオンライン常時監視に移行して行かなければならない。
図 8.2 : 実際の装置設置からオンラインサンプルを想定する
■ ISO4406:製造ライン上での自動検査を実現したオンラインコンタミ監視システム
当社が発明した「PDS.TM」(図 10)は、短時間で測定できるオンラインパーティクルセンサを利用し、検査室に抜き取り品のオイルサンプルを運ぶこともなく、生産タクトタイム内で、生産ラインにて製品流体内に集められた異物を自動的に判定することができる。人間でいうと、自動採血し同時に診断結果もリアルタイムで表示する装置である。その測定結果は、前述した国際汚染度判定基準 ISO4406 で表示判定する。この画期的なシステムは、2016 年からドイツ系大手自動車のトランスミッション生産ラインや F1 バルブ出荷品質監視などで運用が始まっている。重要なのは、オンラインコンタミ監視装置がISO11943「液体用オンライン式自動粒子計数システム」に準拠された校正機器であるかだ。自動粒子計数法というと ISO1171 での校正方法が利用されてきたが、これはボトルサンプル方式での校正方法である。オンラインでの粒子計測の妥当性評価をクリアしたISO11943 が、オンライン常時監視の最適機材であることからの理解が必要である。
図 10 : 世界初、自動車製造ライン向けオンラインコンタミ監視システム「PDS.TM」
①駆動系ユニット製造での活用
自動車部品の中でも AT/CVT など最新のトランスミッションは、リニアソレノイドやベルトを中心に、シビアなコンタミ管理が必要な「油圧」「軸受」「歯車」を備えている。この AT/CVT とその要素部品において、品質や性能に甚大な影響を及ぼす微小な残渣やミクロン単位のオイル中異物をコントロールする必要がある。元々、これら製品の製造プロセスで混入するコンタミを、自動で常時監視・全数検査を可能にするために「PDS.TM」は設計開発された。この装置は、他精密機械産業において 25 年以上にわたり、1000 社を超える先進企業で「オンライン粒子計数法」を実現させ、先端の異物の監視・改善に特化してきたインテクノスで完成した実用性の高いシステムである。「PDS.TM」は、AT/CVTの出荷機能テスタのみならず、各要素部品の試験機や各トランスミッションフルイドの給油配管やタンクのコンタミも、リアルタイムで自動監視できる。バルブ・クラッチ・トルクコンバーター・ポンプ・軸受・歯車・給油など、製造段階でのより高い清浄度数値管理と清浄化において大きな技術貢献をしている。
②その他自動車部品での応用
自動車業界のコンタミネーションマネージメントの強化加速は、高効率・高機能・乗り心地・低燃費といった新たな技術の取り組みによる、小型で複雑な機構への進化が産んだ副産物である。それは、前述したトランスミッションのみならず、エンジン・ブレーキシステム・ステアリング、そして部品洗浄検査、塗装やプレス前の車体洗浄常時評価システムにも転用されている。この PDS.TM は、汚染測定検査デバイスとして、その製造工程におけるプレス機械やアルミダイキャスティング設備機械の油圧作動油の汚染管理にも最適であり、生産設備のダウンタイムを回避できる有効性が評価されている。
「自動車業界の異物管理」まとめ
第1項「自動車部品清浄度検査の標準化」・第2項「駆動系ユニットの異物検査動向」と、すでに始まっている検査方法の標準化について記述したが、現状を診断してみると、高い確率でいくつもの製造プロセスでは清浄度改善の必要性が明らかになる。多くの自動車会社では、品質保証部門や生産技術部門がより微少なコンタミの専門的な検査・改善知識もなく清浄化の任に当たる為、抜本的な検査改善に及ばない結果となっている。理由は様々挙げられるが、バッチ検査やボトルでのオイル計測、フィルタの選定や設置方法が正しくなかったり、ミクロンレベルのコンタミ管理に関する知識や経験、教育の不足が特筆されるだろう。悪い例として、トランスミッションフルイドに深層濾過構造のフィルタを使用
したり、エレメントの選定ミクロンを細かくするだけのあまりに専門性に欠ける改善を実行してしまうケースがある。本質的な監視・改善に取り組むべきだ。部品清浄度を厳しくしても集合体内部ののオイルが汚かったら、信頼性はあがらない品質保証にならない事実にも目を向けるべきだ。
インテクノス・ジャパンは、宇宙防衛・フォーミュラーワンをはじめとした要求清浄度が高い業界でコンサルテーションを行い、その専門的な知識や経験で確実な改善技術を提供してきた。このコンタミネーションマネージメントの先端かつ本質的な技術を日本の主産業である「自動車業界」に提供し貢献すべしと技術の啓蒙活動から奉仕している。自動車業界が今後も新たな技術や先端の部品開発・採用に向かうのであれば、品質や性能に影響を与えるコンタミの粒子径・濃度レベルがより一層シビアになるのは必然である。日進月歩で技術向上を遂げている自動車製造業界において、新しい清浄度監視技術や清浄化に向けた正しい改善技術こそが、製品の信頼性を保証していく核心的な技術なのである。
関連機材・サービス: MicroQuick PDS.TM 受託分析サービス
参照文献:
“Standardised Component Cleanliness Testing” by Markus J. Heneka (RJL Micro & Analytic),
2 March 2016.
(VDA19.1) Inspection of Technical Cleanliness – Particulate Contamination of Functionally
Relevant Automotive Components, 2nd Revised Edition, March 2015.