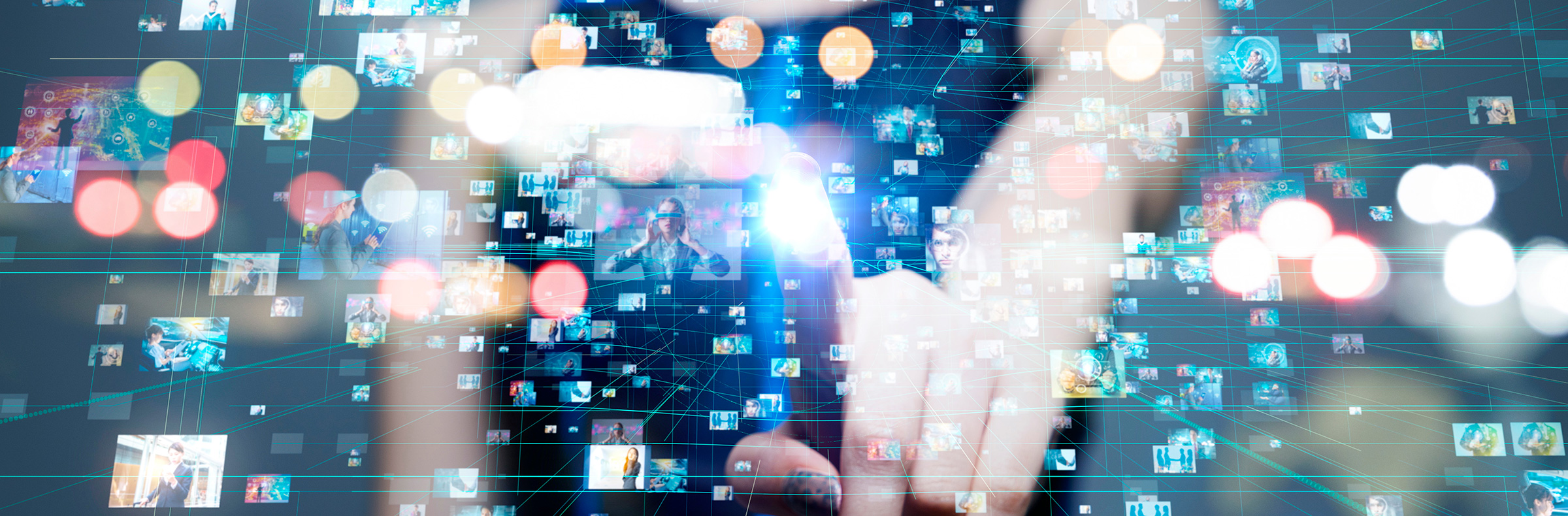
技術情報
2025.02.14
ドイツをはじめとした欧州の自動車業界では、かつてよりサプライヤに対する品質要求のなかで、部品の「清浄度検査」や製造プロセスの「清浄度管理」が求められてきました。
自動車メーカーからフローダウンされる一般要求には、アメリカ発祥のIATF16949や各メーカーの独自規格が含まれ、これらへの適合に奮闘されてきたサプライヤも多くいらっしゃることと思います。
また、欧州の自動車メーカーや大手車載メーカーが要求するVDA(ドイツ自動車工業会)規格では、品質保証のパート4やプロセス監査のパート6.3などへの適合が、越えなければならないハードルとなる場合もあることでしょう。
そんななかで、冒頭の清浄度に関する要求事項においては、部品単体の機能や周辺部品を含めたアセンブリへの影響を考慮し、部品の外観や内部に付着する異物、つまり「汚染粒子」の検査を求められることが、世界的にも当たり前となってきています。
そして、クリーンな部品の証明を求めるニーズの背後には、社会や人々に向けて利便性とともに安心と安全を届けるため、サプライチェーン全体で「クリーンなものづくり」をおこなうことへの期待が込められているはずです。
本稿では、メーカーとサプライヤ双方の持続的なビジネスにかかわるそのような清浄度の検査及び管理について、今や国際的なガイドラインとなったVDA 19.1/ISO 16232及びVDA 19.2の要点を踏まえつつ、お話しします。
自動車メーカーや車載メーカーからVDA 19.1/ISO 16232に基づく清浄度仕様書やCCC(コンポーネント・クリンリネス・コード)への適合を求められた場合、製品もしくは工程途中のワークに対し、「表面清浄度」の検査をおこなわなければなりません。
同時に、そのような清浄度の出来映えに対する要求事項が存在した場合には、製造プロセスの過程で出来映えの安定性や信頼性を左右する「汚染リスク」の管理が必要となります。
サプライヤが顧客や市場の期待に応えるには、これらを総合的に捉えて製造プロセスの「清浄度管理」を検討しなければなりませんが、そのときに一つの拠り所となるのがVDA 19.2です。
VDA 19.2は、部品の「組立」を対象として書かれた規格ですが、異物を付着させない製造プロセスを目指すうえで、あらゆる工程のリスク管理に適用できます。
ここで「異物」と呼ばれる汚染物質の定義が重要になるのですが、VDA 19においては、概ね標準分析検査の対象となる50µm以上、もしくは拡張分析検査の対象となる5µm以上の「マクロ粒子」を指します。
したがって、製造プロセスにおいても、このマクロ粒子の汚染リスクを管理する必要があり、逆に言えばそれよりも小さな浮遊微粒子を管理することは、多くの場合に求められていないどころか無駄な投資と見做されてしまいます。
つまり、出来るだけキレイではなく、「必要なだけキレイ」が求められており、これを出発点として、いつもキレイな製品を造るためのリスク管理を確立することが重要なのです。
とはいえ、まずは清浄度検査を正しくおこなえなければ、製品やワークの清浄度を評価することができませんので、次項では検査の方法と注意点からお話ししていきたいと思います。
部材やワーク、製品がどれだけ清浄な状態であるか、それを知るためにおこなわれるのが「清浄度検査」です。
表面に付着している汚染粒子を液体で洗い流し、メンブレンフィルタに抽出して光学分析や元素分析をおこなう、もしくは液中でサイズごとにカウントする方法が一般的です。
これら従来のやり方は、以下の記事にも書いているので、参考にしていただければと思います。
自動車部品清浄度検査の標準化と駆動系ユニットの異物検査動向 VDA19.1(ISO16232)
最近では、ASTMやISOの技術標準に倣い、自動車を含めた様々な業界で「テープリフト法」を用いた検査方法が確立されつつあります。
テープリフト法とは元来、製品検査だけでなく製造環境の「表面清浄度」をモニタリングするために広く活用されてきたサンプリング方法であり、VDA 19.2やISO 14644-9(クリーンルーム及び関連制御環境における表面清浄度のアセスメント)にも関連する手順が記載されています。
テープリフト法の手順や検査機材については、以下をご参照ください。
この方法では、あくまでもプロセス管理の一環としておこなわれる「清浄度検査」を誰でも簡単に実施でき、大掛かりな検査装置を備えた試験所や厳格な抽出液体の清浄度管理など、煩雑でコストのかかる準備過程をスキップできます。
ただし、いずれの方法を用いる場合にも、対象の清浄度に及ぼされる外部要因の汚染影響を避けるため、検査環境の清浄度管理はVDA19.2を参照してある程度おこなわなければなりません。
ここでもやはり、空気清浄度クラスやクリーンエア技術が求められることは少なく、「マクロ粒子汚染」のリスク管理が主要な要求となってくる点にご注意ください。
VDA 19.2において製品清浄度の達成を妨げる汚染リスクは、製造プロセスにかかわるヒトとモノによって生じ、これらの要因が適切な状態であることを検証するために、「表面清浄度」と「沈降粒子」の測定が求められます。
なお、リスクとなるマクロ粒子汚染のメカニズムは、空気に浮遊するより小さな粒子とは異なり、空調制御システムやHEPAフィルタでは解消できないことから、優れたクリーンルームの性能が大きく意味を成しません(これに関しては、以下も参考にしてください)。
そのため、施設性能に依存しない適切なプロセス設計と要員への訓練、地道な実践活動と測定及びアセスメントの継続を通じたフィードバックにより、汚染リスクを抑え込まなければならないのです。
インテクノスのコンサルティングでは、顧客企業がおこなうこれらのプロセスを支援し、エンジニア及び管理者に向けた定期教育も提供しております。
ちなみに要員への訓練は、VDA 19.2の主要な要求事項であり、元来、この完成度が製品清浄度を最も大きく左右するといっても過言ではありません。
ここまでを含めると、製造プロセスにおける汚染リスクの管理やVDA 19.2という規格は、実は非常に奥が深いので、本稿ではこの後、検討初期に重要なクリーングレード(CG)という考え方に的を絞って深掘りしたいと思います。
クリーンルームはわかるけど、「クリーングレード」って何ぞや?と思われる方も多くいらっしゃることでしょう。ずばり、このクリーングレード(CG)とは、クリーンルームと一般環境の中間を含めて定義される製造環境の清浄度等級です。
中間って?・・・空気清浄度クラスではありません。あくまでも製品にとっての汚染リスクに焦点を当てた管理(制御)レベルの違いを指します。
したがって主に、「マクロ粒子汚染」のリスクをどの程度まで許容して制御するか、それによってCGを高く設定したり、低く設定したりするのです。
CGによる違いは以下を基礎的な参考として検討されます。
CG 0:非管理ゾーン
CG1:清浄度ゾーン
CG2:清浄度ルーム
CG3:クリーンルーム(一般的にはISO 14644への準拠)
やはり中心となるのは、ヒトとモノに関する規則や移動制限であり、これらを確立するにはマクロ粒子汚染のリスクに対する正しい測定とアセスメントの方法を理解する必要があります(インテクノスはセミナーを通じ、国際規格に沿った方法論の解説を提供しています)。
そして、これらの適切さを実証し続けるために、製造プロセスにおける定常的な測定を行い、CGを含めた制御の結果的な汚染リスクを「監視」することが要求されます。
言ってしまえば、製品やワークの清浄度検査も「監視」の一環であり、品質保証というよりは品質管理、もっと言えば、品質リスク管理のためにおこなわれます。
でもその出来映えだけがわかっても、どのような状況でそれが成り立っているのかわからず、悪化したときや既に改善が求められているときに、何をどのように変えれば良いのかわかりません。
ISO 9001の予防的管理を引き合いに出すならば、品質マネジメントシステムにおいては元来、リスクに基づく考え方が必須であり、出来映えの悪化を引き起こす可能性のある要因を明確にし、その影響を最小限に抑えるべきでしょう。
ここで、製品清浄度の悪化を引き起こす可能性のある要因(リスクファクタ)というのが、前項までに登場した製造プロセスのヒトとモノです。
それらがあくまでも製品清浄度に関連してどのような状況にあるのか、それを常に監視して悪化を「未然に防ぐ」ことが重要であり、そのためにはリスクファクタに関連する「表面清浄度」と「沈降粒子」を定常的に測定しなければなりません。
また、そのような監視を通じ、各リスクファクタの状況変化による影響を評価することで、今よりも出来映えを良くしたり、もっと効率的に達成する糸口もつかめるはずです。
VDA 19.2において推奨されている「表面清浄度」の監視では、清浄度検査のときと同様の測定方法を用いますが、製造プロセスにかかわるあらゆるヒトとモノに関連する表面が対象となります。
「沈降粒子」の方はというと、従来の粒子トラップと呼ばれる方法では発塵のタイミングがわからず、リスクファクタの不適切な動きを発見することが困難なため、ISO 14644-17という国際規格に基づいた「リアルタイムPDR監視」を推奨します。
リアルタイムPDR監視については、以下をご参照ください。
また、インテクノスの診断サービスでは、専門員による現場での汚染リスクの測定に加え、製造プロセスに潜むリスク要因の抽出をおこない、監視のポイントを含めた改善アドバイスを提供しています。
サービスのご用命をご検討の際は、もしくは本稿に関するご質問、異物のお困り事などございましたら、いつでもお問合せをお待ちしております。
高木 篤 / コンサルティングTOPチーム ― TOBIRA ―