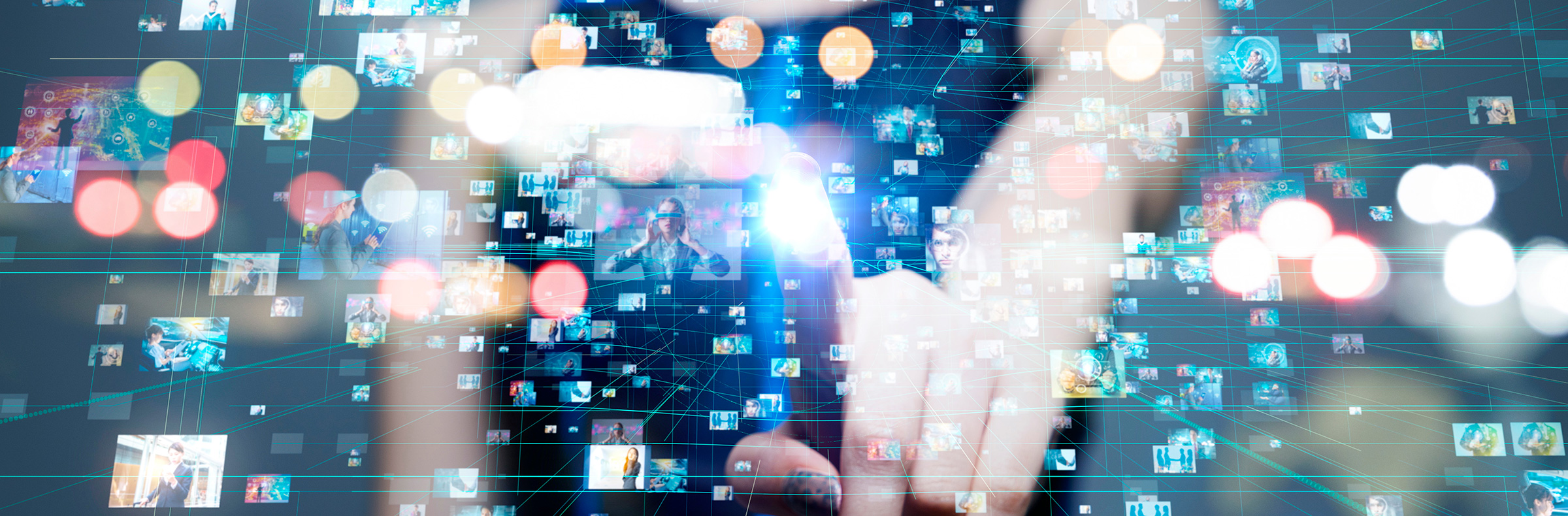
ブログ
2024.11.25
精密機械部品や半導体、電子デバイス、医療機器など、汚染に脆弱な製品やその中に組み込まれる部品の多くは、製造プロセスにおける組立前の「洗浄」により、必要な表面清浄度を確保します。
「表面清浄度」には一般に、表面上の粒子状物質を定量化したSCP(Surface Cleanliness by Particle concentration/ISO 14644-9)と、化学物質を定量化したSCC(Surface Cleanliness by Chemical concentration/ISO 14644-10)の2種類があります。
この記事では、表面上の汚染粒子、いわゆるパーティクルの除去を目的としたウェット洗浄の工程について、「SCP」の目標値に対する妥当性評価の方法と、その達成を妨げる再汚染リスクへの対策を、国際的な汚染制御ガイダンスや当社ノウハウをもとにお話しします。
洗浄工程をお持ちの皆様は、ワークが上手く洗い上がっていることをどのように評価していらっしゃるでしょうか?
対象となる表面や汚染物質の種類に応じ、顕微鏡での観察やSEM-EDX、FTIRなど、様々な分析・評価方法を用いられていることと思います。
中には、製造プロセスの全体を通した出来映えとして、最終的な目視検査でチェックしている場合もあるのではないでしょうか。
しかし、多種多様な分析方法を駆使しておこなう評価には相当の時間が掛かり、人の視力など力量に大きく依存する手法では正確性に欠けてしまいます。
それに、洗浄後のワークが他の工程やハンドリングによって再汚染されるリスクを考慮すると、洗浄直後の状態でなければ純粋な洗浄工程の妥当性を評価することはできないでしょう。
ではどのようにして評価すべきか、国際規格の観点からお話ししますと、パーティクルの除去については、ISO 14644-9およびISO 14644-13の活用を推奨します。
これらの規格をすべて読むのは大変なので、妥当性評価におけるポイントのみを抽出してお話しします。
まず、評価方法の概要としては、洗浄直前の表面清浄度(SCP)を測定し、同様に測定した洗浄直後の表面清浄度と比較することで、何パーセントの付着粒子を除去できたか(洗浄効率)、また、目標値に対する達成度は如何ほどか(妥当性)を数値化します。
洗浄効率 = 1 - 最終SCP/初期SCP × 100 [%]
妥当性 = 最終SCP/目標SCP × 100 [%]
初期SCP: 対象表面における洗浄直前の付着粒子濃度 [個/㎠]
最終SCP: 対象表面における洗浄直後の付着粒子濃度 [個/㎠]
目標SCP: 対象表面において洗浄直後に目標とする付着粒子濃度 [個/㎠]
ここで、洗浄の妥当性を評価するために必要となる目標SCPは、最終製品や部品機能への影響評価をもとに、決定しなければなりません(影響評価については、別の記事で詳しく解説する予定です。)。
また、洗浄の「直前」と「直後」でSCPを測るには、工程の存在する現場で実施可能な測定方法でなければなりません。
測定方法については、こちらをご参照ください。
対象表面に付着した汚染粒子を除去するには、まず始めに表面から粒子を引き剥がすことが必要です。
引き剥がすために用いられる技術は一般に、液体に付与された超音波や圧力リンスなどの機械的エネルギーに加え、洗浄剤の化学的エネルギーを利用し、温度と時間のパラメータを含めて制御されます。
ここで、すべての汚染粒子を引き剥がすことができれば、対象表面はキレイになると思っていらっしゃらないですか?
すみません!それは間違いです。引き剥がした汚染粒子を対象表面の周りから「除去」しなければならないのです。
つまり、洗浄液中からパーティクルを取り除くことが必要です。洗浄液を槽に溜めず掛け流す場合でも、含まれるパーティクルを予め除去しておかなければなりません。
除去する技術とは、一言で言うとフィルトレーション、すなわち「ろ過」のシステムを正しく備えることです。
洗浄液が汚れていると、せっかく汚れを落とした表面が「再汚染」されてしまいます。洗浄液中のパーティクルを適切に除去し、このリスクを低減しましょう。
まず、洗浄液を槽に溜める場合には、槽内を「循環」させながらろ過する方式をとります。これは、対象表面から引き剥がした汚染粒子を槽内に滞留させることなく、循環回路に取り付けたフィルタで除去するために必要なことです。
そして、多くの場合に汚染粒子は洗浄液よりも密度が高く、粒子サイズが大きくなるほど静的な状態において槽の下部に沈降しやすくなります。
一般的な洗浄装置の槽内循環には、槽上部の液面から排液するオーバーフロー方式が用いられますが、これだけではサイズの大きな汚染粒子や密度の高い金属粒子などが槽内に滞留しやすいので要注意です。
槽の底部を円錐形にして給液口にはディフューザを設置し、穏やかに流れ込んだ洗浄液が底部からもフィルタへと上手く循環するように設計することがポイントです。
このようにして、適切なろ過システムの構造を設計できれば、あとは対象表面から汚染粒子が引き剥がされている時間に、適切な循環流量とろ過効率を確保することで、再汚染のリスクを低減することができます。
適切な循環流量は、同じ容量の槽であっても、対象表面の汚染度合いや洗浄工程のタクトタイム、そして、フィルタのろ過効率によって大きく左右されます。
ここで、最も確実なのは、循環流量をある程度調整可能としたうえで、高いろ過効率を発揮できるフィルタを選定しておくことです(フィルタの選定については、ご要望に応じて解説させて頂きたいと思います。こちら からお問合せ頂いてもお答えできます。)。
また、洗浄液を槽に溜めない場合でも、貯蔵タンクでのキドニーループフィルトレーション(オフライン・マルチパスろ過)や給液前のラストチャンスフィルトレーション(インライン・シングルパスろ過)、リサイクル回路のろ過などに、流量特性や捕捉容量にも優れた「高性能フィルタ」を採用しておくに越したことはありません。 その際、ろ過精度○○µmや90%除去・・・などを当てにするのではなく、対象の液体やシステムに合った本物の高性能フィルタを選び抜くエンジニアの力量が問われます(決して大袈裟ではございません|д゚)。
冒頭にSCP測定による洗浄工程の妥当性評価についてお話ししました。この方法で、出来映えについては評価できるのですが、いざ結果が悪かったときやタクトタイム短縮などの改善を検討したいとき、これだけでは情報が足りません。
なにより、重要なフィルタの性能が、汚染粒子の捕捉量(本来、差圧ではわかりません)やフィルタ自体のシール品質(ものにより、ばらつきがあります)によって変動してしまうため、これをモニタリングする方法が別途必要となります。
シンプルに、「洗浄液中のパーティクル」をモニタリングすることで、出来映え評価と並んで最も重要な情報を得ることができます。
液中パーティクルの変動をモニタリングすれば、フィルタの品質不良や劣化を検知できるだけでなく、洗浄工程のクオリティやパフォーマンスを改善する糸口が見つかるハズです。
ただし、ろ過システムによる除去と同様に、液中で沈降しやすい汚染粒子(特に10µm以上のマクロ粒子)をモニタリングするには、粒子の振る舞いを考慮した専門的な技術が必要となります。
簡単に言えば、沈降に打ち勝てる速力で吸い込んで検出しなければなりません。そして本来、散乱光ではなく影を捉える測定原理でなければマクロ粒子は検出できず、このことを良く理解していないと誤った結果を信じてしまい兼ねないので、注意してください(キレイだと誤認してしまいます)。
洗浄液中における「マクロ粒子」のモニタリング技術については、こちら をご参照ください。
まとめると、「洗浄前後のSCP」と「洗浄液中のパーティクル」のモニタリング技術を備えてようやく、洗浄工程のモニタリングは問題なしということですね!(あくまで、汚染粒子についてです!)
せっかくワークをキレイにしても、お客様の手元に届いたときに汚れてしまっていたら、意味がなくなってしまいますよね。
なので、洗浄後、出荷までの再汚染に対して、考慮すべきことを簡単にお話しします。当然ですが、洗浄した製品も出荷するまでに汚染されることがあります。
汚染のメカニズムは主に2つ、汚染粒子(空間中の場合、特に5µm以上のマクロ粒子)の「落下堆積」と「接触転移」です。
例えばクリーンルームの様な空気がキレイな環境であってもお構いなしに、作業者や資材の表面に乗った汚染粒子が、これらのメカニズムを繰り返しながら洗浄後の表面に付着します。
2021年にISO委員会は、マクロ粒子の多くが気中パーティクルカウンタで検出されないことなどにより、クリーンルームのクラス管理で示されるよりもはるかに多くの表面汚染が存在することに対し、ISO 14644-17の発行を以て対策技術を世界に提議しました。
そして、粒子堆積率(PDR: Particle Deposition Rate/ISO 14644-17)という指標を用い、「落下堆積」のリスクをリアルタイム監視することが推奨されています(モニタリング技術については、こちら をご参照ください。)。
その原因と結果であり「接触転移」のもとにもなる表面汚染は、SCPを用いてモニタリングすることができます(モニタリング技術については、こちらをご参照ください。)。
これらのモニタリングを通じ、洗浄後の乾燥や検査、包装をおこなう環境、包装材の内側などをキレイな状態に維持管理することが、顧客や市場のニーズと期待に応えるクリーンな製品へと繋がっていくはずです。
高木 篤 / コンサルティングTOPチーム ― TOBIRA ―