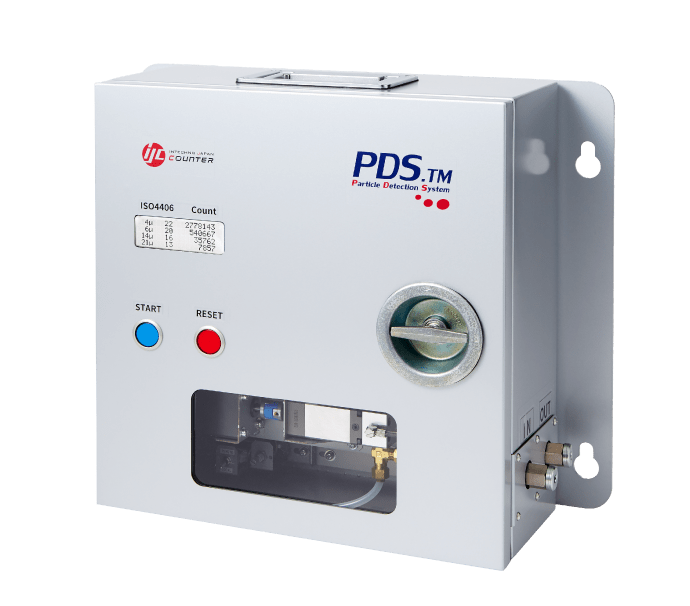
Online Fluid Contamination Monitoring SystemPDS.TM
100% inspection on production line
in 5 seconds
- ISO4406
100% inspection on production line
in 5 seconds
All mechanical products that use oil or fuel, including automobiles, aircrafts, and construction machinery must have appropriate evaluation and flushing at the manufacturing stage. Although manual analysis and gravimetric analysis have been practiced for inspections, with the rise of quality demands in the market, the method has shifted to particle counting methods, inspecting from particle sizes and numbers. Along with the method of analysis, inspection has increased its frequency from a batch inspection and regular laboratory analysis to monitoring within the system.
PDS.TM is an online measuring system that can monitor contamination on production lines and centralized refueling machines. By installing it in the system, fuel monitoring is possible at any time. It is a powerful tool for preventive maintenance that enables real-time inspection of machines and equipment.
As the laser beam projects a moving column of oil, particles are measured by a photo diode that converts light intensity to a voltage output and records against time. The amount of light lost when the particle moves across the window is proportional to the size of the particle and this reduction in voltage is measured and recorded.
Function | Internal automatic flushing / defoaming function |
---|---|
Measurement principle | Light-shielding automatic particle counting method (laser diode) |
Applicable oil type | Mineral oil, synthetic oil, light oil, kerosene |
Applicable standards | ISO4406 grade 7-22 grade |
Particle size | 4 channels (> 4,> 6,> 14,> 21µm (c) |
Result display | LCD display |
Unit flow rate | 60 mL / min (during flushing: 120 mL / min) |
Working pressure | 0.5Mpa or less. Free when output is open to the atmosphere |
Viscosity used | Dynamic viscosity 150cSt * 1 |
Oil temperature rang | Oil temperature range + 5 to + 70℃ (depending on the above viscosity range) |
Power supply | 100-120V (240V is an option) Power consumption: 65W |
Calibration standard | ISO 11943 (using ISO 11171 standard) |
External communication | RS232C |
External output | Analog output 4-20mA (> 4 (A),> 6 (B),> 14 (C)µm (C) pollution grade only) |
External start | Start by connecting contact 1-2 pin |
External dimensions | 410x165x360 (mm) Including flange |
Weight | Approximately 13 kg |
* 1: Liquids with kinematic viscosity exceeding 150 cSt are supported by the high viscosity "PDS.V4" lineup.